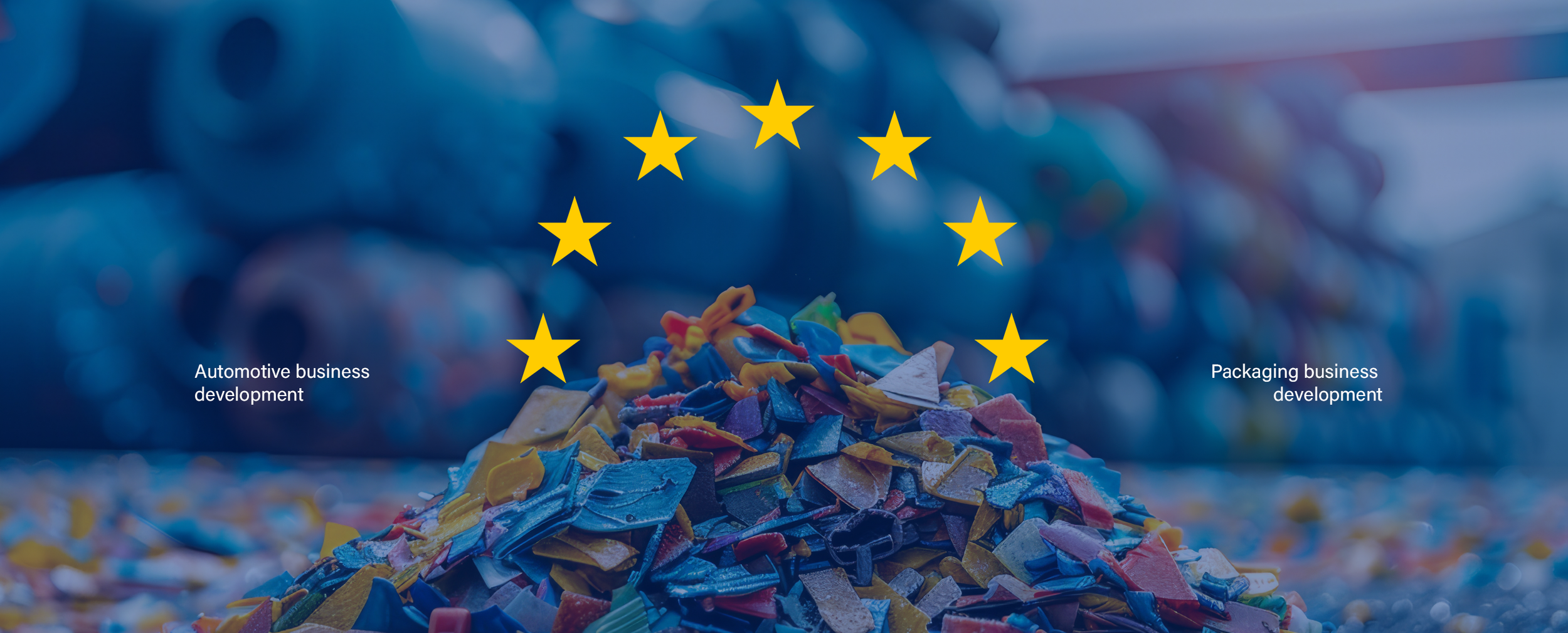
Sustainability, the new paradigm…
New European regulations such as the ELV-R and the PPWR regulation are shaping up rapidly, they are already changing the plastic business and the competitive landscape in Europe. They will be a threat for the incumbent suppliers but also an opportunity to grow business, in any case it is a mandate to innovate.
Packaging PPWR
-
Packaging is by far the largest plastic market segment with 22 MT/y, more than 50% of the European total plastic demand, therefore the most exposed to consumer protest. It was logically the first industry to be “regulated”. The PPWR (Packaging and Packaging Waste Regulations) includes a large spectrum of specific regulations (delegated acts) from Packaging design, material substitutions, new substances of concern (PFAS, BPA), labelling … PPWR covers all flexible and rigid packaging made of any materials (metal, paper, glass, hood,…) as well as composite packaging mixing different types of materials. But the most striking requirement is without any contest the minimum content of post-consumer recycled material (PCR) by packaging unit.
Over the last 10 years the chemical industry has developed new technologies and product strategies to deal with PPWR. Meanwhile the recyclers, the compounders, the film converters and the brand owners are struggling, the post consumer plastic demand remains low and PPWR’s implementation and details remain uncertain : how to turn PPWR to your advantage and prepare for 2030 ?
What impact will this have on the plastic packaging industry ?
-
The PPWR will be shifting in Europe between 10 % to 35% of the plastic raw material source used in Packaging (22 Mt/y) from virgin polymers to recycled polymers.
As of 2030 up to 35 % of packaging made of PCR source will become “specialty plastic” with diverse specifications (tolerances, transparency, strength, MFI) supplied from multiple recyclers or traders.
-
The PPWR “delegated act” dealing with DFR is in progress, it should be frozen by end of 2025 and adopted in 2028. The designers will need to achieve the DFR rating with a minimum of 70% recyclability on a packaging unit level while dealing with mandatory recycled content.
-
Using plastic fulfilling the different regulations will become increasingly complex and expensive, customers and brand owners (e.g. Mars, Nestle, Coca-cola, P&G…) are looking for plastic alternative whenever it is, economically and technically possible.
Paper is the alternative for flexible packaging, the recyclability is given for rigid packaging, but food packaging remaisn the major challenge with coated paper films. Paper films costs and Carbon Footprint are a limiting factors. See the cross-industry alliance of over 100 members representing the entire lifecycle of fibre-based packaging.
-
the DFR regulations will ban some materials used in multilayer design, and favour new mono material solutions such as BOPE, MDO or BOPP . Polymer PCR availability in quality and quantity will be another factor influencing the material selection.
-
Major chemical corporations selling virgin plastics and backward integrated (Total, INEOS, ARAMCO,..) will lose a share of their market and the full control of their raw materials. New “plastic suppliers” controlling PCR source will emerge. For Chemical Recycling, the majors (LYB, BASF, Dow, INEOS,…) are building new capacity, although they will need to secure clean PCR sources to run their CR facilities, As a result new alliances will emerge in the supply chain of the Chemical industry to deal with PPWR.
Automotive ELV R
-
has a bad reputation : CO2 emission, high manufacturing energy bill and visible pollution from End of life vehicles. On the other hand, collecting and recycling ELV is relatively easy, in any case easier than packaging and,it has been operating for decades. It was logically the second large plastic industry to be “regulated” by the European commission after Packaging. The ELV directive is at this stage “just” a directive, adopted in July 2023 for all European countries; the amendment process is ongoing and the EU commission vote to turn it into a regulation is not fixed yet ( 2025 ?). Unlike the PPWR , the ELV Directive is relatively focussed : a recycled plastic content of 25% PCR plastic by vehicle, including 6,2% of automotive closed loop PCR content.
In the Automotive industry, the ELV R is not yet voted, it is being reviewed and amended. The minimum PCR content by vehicle will be a great challenge whatever the content, specifically for the “closed loop” automotive PCR. Some plastics used in automotive will gain market share as they will be more “recyclable” than others. Automotive PCR plastic sources will be short and expensive and become an issue for the OEM to comply with the regulation. Where to use PCR plastics ? A good technical understanding of the automotive by application segment is critical.
What impact will this have on the Automotive plastic industry ?
-
The automotive industry is sourcing 4,4 Mt of plastics in Europe, mostly specialty plastics with tight specifications that need to be available for the lifetime of the vehicle, ideally globally.
Automotive OEM and Tier 1 have been using industrial plastic waste for cost reductions reasons (5 to 10% by vehicles). nevertheless the transition to 15 of 25 % of PCR , if confirmed will be a challenge for procurement, supply safety, quality, cost competitiveness and price stability.
-
The regulation implementation pace will be slower in automotive than for the packaging industry, therefore Automotive OEM and tiers will need to start their approval process earlier to be ready for 2032 .
The technical requirements (heat stability, paintability, aesthetic, impact resistance, odor, aging...) will determine the preferred application segments and respectively the optimum level of PCR quality required.
As the ELV target is a weight content, the OEM will focus on the heaviest application and where PCR source are the most available (From other industries source as well as from Automotive ELV).
Bumpers, instrument panels, door panels made of PP is the logical place to start but shortages of High quality PP PCR will push the industry to look at other applications such as seats , trunk doors, carpets , spoilers , rear lights and under the hood…
-
Reaching 20 or 25% of recycle content by vehicle is opening many different scenarios. which applications, materials, technology (MR vs CR) and design ?. Although PP PCR seems to be the low hanging fruit, the supply / demand balance of ELV PP and its poor quality may actually favour alternative materials.
The “recyclability” of plastics in Automotive will become a new attribute in the inter-polymer competition.
-
To reach the specifications of Automotive applications, compounding PCR with Virgin plastic and additives is the safest solution. The formulation expertise represent a barrier to entry for new commers. Large compounders with access to PCR are learning fast and will offer a competitive advantage becoming direct Automotive plastic suppliers in specific applications.
In any case a ELV regulations will change the supply chain game in the coming 10 years, there will be winners and losers.